既然机床加工出零件的精度永远低于机床本身的精度,那高精度的机床是怎么产生的呢?这是一个比较复杂的问题,听起来像是一个悖论的循环。实际上这个问题在我读书的年龄,就有在书中见到,记得那时就有人提出,第一台机床是怎么产生的?精度是多少?难道第一台机床精度最高吗?
其实机床精度的提高有一个循环的过程,是一种螺旋上升的过程,也就是一个不断的修正和补偿来提高精度的过程。我记得那时的书里就是这么说的。
我记得那本书里说的例子是丝杠的螺距,一根丝杠,低精度的机床加工出来,螺距之间尺寸是不等的,任意两点之间的螺距误差都比较大,但在一个范围之内,这个范围就是误差,实际就是精度,那么怎么拿它做出来一个比它精度高的丝杠呢?于是就提出了一个方法,就是进行修正和补偿,对于正偏差采取人工修磨,负偏差采取加大螺母的长度,覆盖影响精度的负偏差,使其能提取出大部分精度好的样本,制作出精度更好的丝杠。如此不断的循环往复,就可以造出精度更好丝杠。
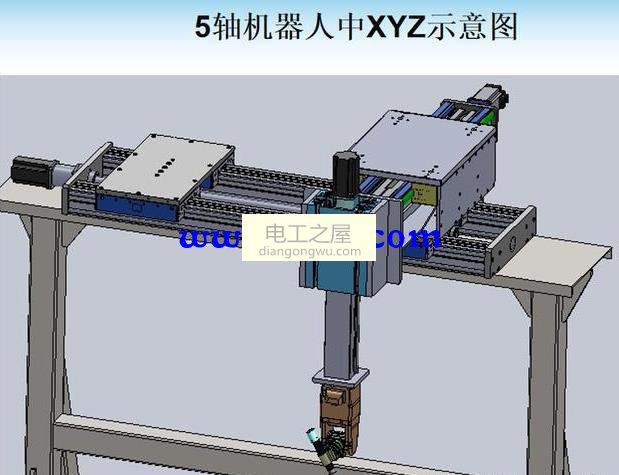
这个原理和加工一个平台,通过一个小的样块,不断的对比刮研使平面精度越来越高原理是一样的。
所以精度能不断提高的精髓在于人工的修正和补偿,没有人工的干预,当然不能造出高于机床精度的产品。
这是机床发展早期使用的方法,有它的发展极限,到达这种方法提高精度的极限之后,就要寻找新的方法,因为影响精度的因素这时候也变了,所以方法就失效了。
后来就兴起了材料科学,使用适合的材料来提高精度,比如低温度系数材料,耐磨材料,低时效材料等,进一步提高机床的精度。
随着近代各个周边科学技术的不断发展,机械制造领域的测量手段不断提高,动力驱动系统的数字化,就进入了通过计算机软件和高精度的测量手段,通过机械补偿动作提高精度的阶段,使机床的加工精度进一步提高。
机械加工精度依赖于基础的线,面,园等基础线和面的精度,最基础的基准,来自于水平和垂直,这两方面的测量手段每提高一次,相应的机床的设备就有了新的目标,尤其是大型设备,精度就会再得到一次提高。